高效精准的智能计件软件全方位赋能企业生产效能跃升
19429202025-03-23PC软件11 浏览
一、传统计件模式为何成为效率“绊脚石”?
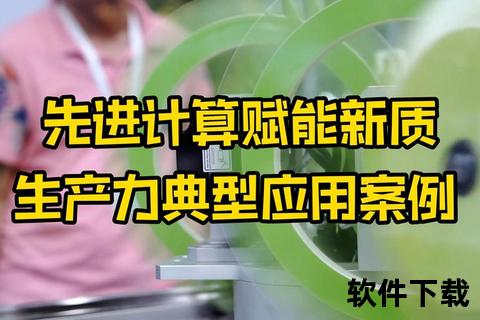
在制造业车间里,一个争议始终存在:手工记录计件数据与工人工资核算的模式,究竟是“成本控制手段”还是“效率黑洞”?某五金加工厂曾因计件工资核算错误引发集体停工,经调查发现,手工记录的生产数量与实际库存相差23%,工时统计与设备运行数据存在15%的偏差。这种因计件管理粗放导致的纠纷,在2024年中国制造业协会统计中占比达37%。
传统模式暴露三大致命缺陷:纸质单据流转造成数据延迟超48小时,人工计算错误率高达8%-12%,多工序协同生产时进度追踪失效率达60%。而高效精准的智能计件软件通过扫码报工、自动排产、实时看板等功能,将上述问题化解于无形。浙江某汽配企业引入智能计件系统后,仅用3个月就将工资核算周期从7天压缩至实时生成,工序流转效率提升40%。
二、数据驱动如何重构生产决策链条?
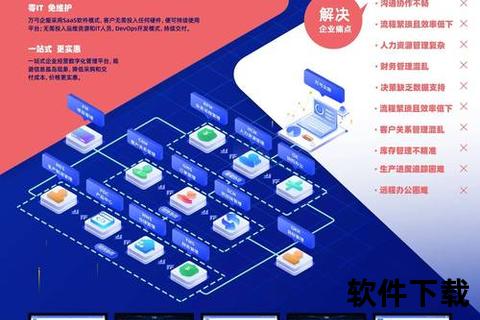
当东莞某电子厂遭遇“旺季爆单、淡季闲置”的困境时,其部署的智能计件系统展现出惊人价值。系统通过采集12个工序的532组实时数据,结合历史订单规律,自动生成动态排产方案,使设备利用率从68%跃升至89%,紧急插单响应速度提升3倍。这印证了高效精准的智能计件软件全方位赋能企业生产效能跃升的核心逻辑——将离散数据转化为决策智慧。
该系统构建起三层数据价值网:基础层通过IoT设备自动采集200+维度的生产数据;分析层运用机器学习预测工时偏差,准确率达92%;应用层生成可视化看板,指导现场调度。青岛某纺织企业借助该体系,成功将次品率从5.7%降至1.2%,年度能耗成本节约超80万元。
三、行业差异化需求如何精准满足?
家具制造业面临的挑战极具代表性:某实木家具厂需要同时管理32种木材、78道工序、200+款产品,传统ERP系统根本无法适配其非标生产特性。引入模块化智能计件软件后,通过配置化界面自主搭建工序流程,结合3D建模实现材料利用率可视化,使木材损耗率从18%降至9%,定制订单交付准时率提升至98%。
不同规模企业的需求呈现明显差异:
中小微企业:管家婆工贸等轻量化系统支持扫码报工、移动端核验,实施成本控制在万元内
大型集团:西门子Opcenter等平台实现从报价到交付的全流程数字化,使新品导入周期缩短40%
离散制造:橙子MES等解决方案支持多工厂协同,某汽车零部件企业借此实现5地工厂产能平衡
破局之路:智能升级的三大实施准则
在深圳某智能硬件企业的转型案例中,三个关键决策点值得借鉴:首先选择支持API接口的云原生架构,确保与现有ERP、WMS系统的无缝对接;其次建立数据治理委员会,规范37项数据采集标准;最后分阶段实施,先从核心车间试点再逐步推广。
企业实施智能计件系统应遵循“3C原则”:
1. 兼容性(Compatibility):确保系统支持SCADA、AGV等智能设备接入,如日立方案通过Dynamics 365整合10类工业设备
2. 可配置(Configurable):选择支持BOM自由组合、工序灵活调整的系统,某医疗器械企业借此快速适配新产品线
3. 持续进化(Continuous Evolution):定期进行系统迭代,某光伏企业每季度更新算法模型,使排产准确率持续提升
高效精准的智能计件软件全方位赋能企业生产效能跃升已成必然趋势。从广东电子厂到东北装备制造基地,这场由数据驱动的生产革命正在重塑中国制造的核心竞争力。当系统看板上跳动的不仅是数字,更是企业转型升级的生命线时,智能化已不再是选择题,而是生存发展的必答题。